SHARE
Rapid Prototyping with 3D Printing and Additive Manufacturing
3D printing or additive manufacturing is manufacturing objects without the use of dies, molds, or machining. Instead, it lay down successive layers of material under computer control by using a 3D model. The below figure represents the process flow of rapid prototyping.
Source: http://dupress.com/articles/additive-manufacturing-3d-opportunity-in-aerospace/
There are several advantages of 3D printing compared to traditional manufacturing processes due to lightweight, less waste generation, and the possibility of material and product optimization ultimately reducing cost components. There are lots of applications of 3D printing in product development, manufacturing, operational, and also after service stages.
Let’s take an example of product development. See the below figure with three structural elements that are designed to carry the same structural loads and force. Virtually it is possible to manufacture items with any geometrical shape by 3D printing. This enables optimum solutions for different applications. Also, the design takes less time and cost compared to traditional product development techniques which typically waste thousands of material and labor hours before becoming reality. The far smaller item with a complicated shape is 75% smaller and 40% lighter which is developed using an optimized 3D printing technique.
Source: http://www.sustainablecitiescollective.com/grmeyers/1078161/3d-printing-reduces-building-costs-weight-and-waste
If we move on to the manufacturing stage, the raw material cost is the main cost component. Traditional manufacturing chips away raw material until it gets the required product while 3D printing adds raw material as needed. This is how 3D printing reduces wastage while manufacturing. Especially, when considering valuable raw materials like titanium, this will be a very beneficial technology for the space industry for reducing manufacturing cost.
In the operational phase, the operating cost (eg. fuel cost of a vehicle) is the primary concern.
The weight of accumulated parts is a critical factor for example in an aircraft. It has been found that using 3D printed metal parts can reduce the weight of an aircraft by up to 7%. 3D printing of key parts of aircraft can cut down the fuel consumption by approximately 6.4%
Source: http://3dprint.com/71279/3d-print-aircraft-weight/
Another example is the Blade; the first 3D printed supercar.
It is made by series of chassis parts held together by carbon rods which is like a Lego. The fueling 700HP engine can be done either by natural gas or gasoline. The weight of the car is just 1400lbs which is 90% less than some modern cars.
Source: http://www.dailymail.co.uk/sciencetech/article-3138145/The-gas-powered-3D-printed-supercar-0-60-TWO-seconds.html
The items which have gone through the above life cycle end up as broken or non-functioning someday. Therefore, after service is not an exception for 3D printing. Suppose a refinery or some other industrial plant has a broken critical component which is to be replaced soon. If this part is no longer being manufactured and not available in the market what 3D printing technology can do for reducing the replacement time and cost?
Just a few steps;
Source: http://www.slideshare.net/patrickseaman/3d-printing-edge-manufacturing-white-paper
In a recent survey of more than 100 industrial manufacturers, two-thirds were already using 3-D printing at least one of the production phases. However, most of the applications are dedicated to rapid prototyping only. Source: http://www.pwc.com/us/en/technology-forecast/2014/3d-printing/features/future-3d-printing.jhtml
Therefore there is a big space to improve further! Are you interested in 3D printing and rapid prototyping? See what ennomotive has to offer.
Check out our engineering challenges!
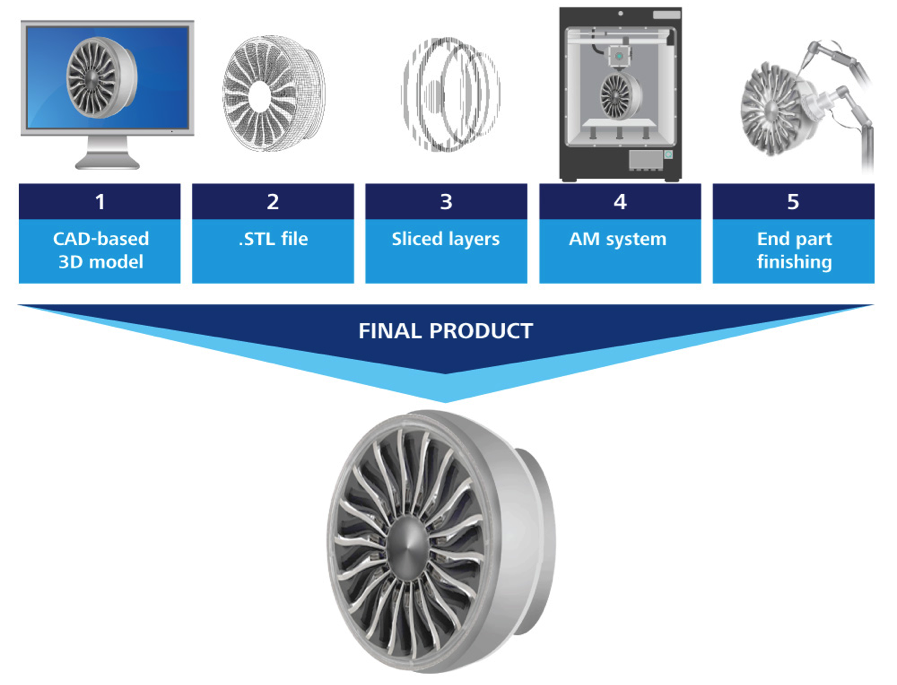
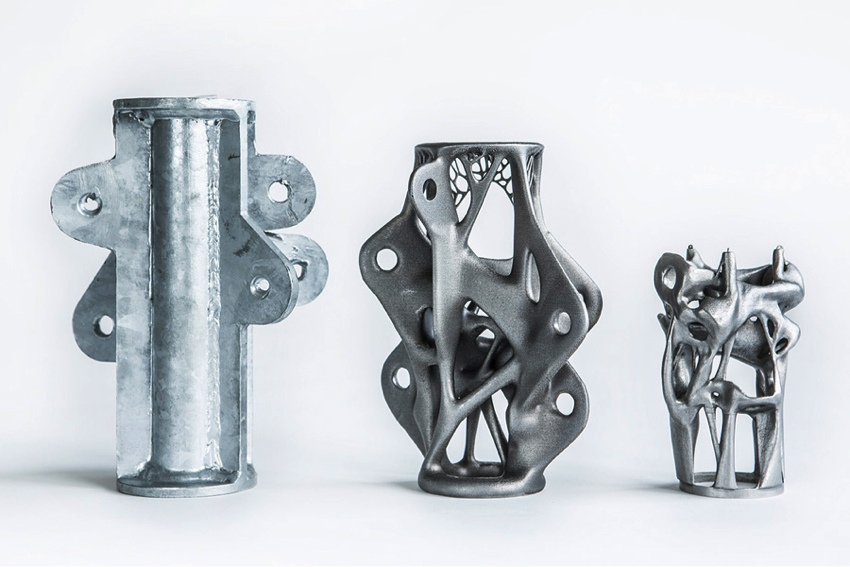
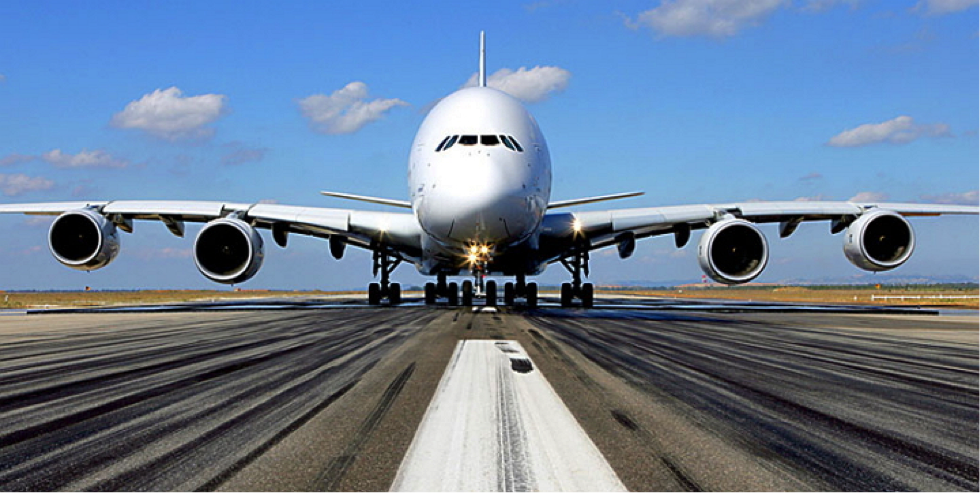
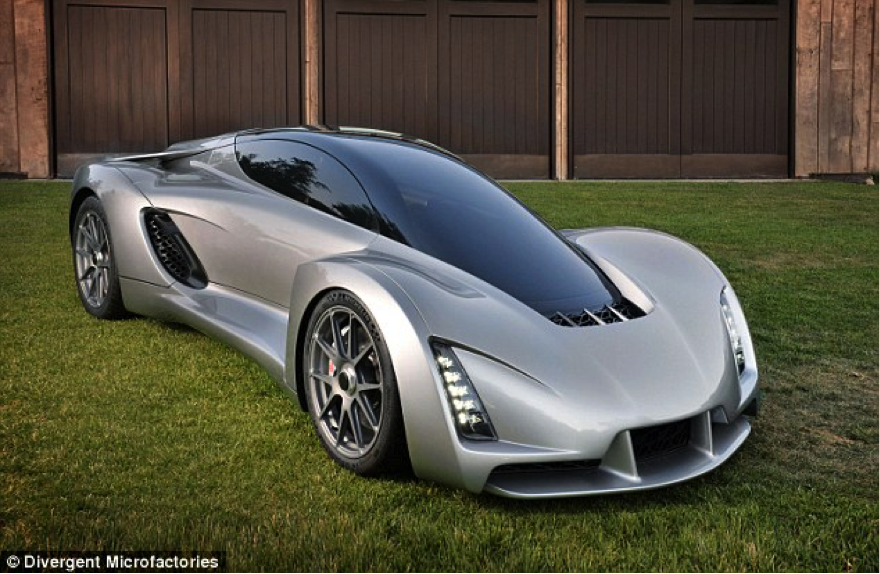
- An on-site engineer can provide drawings or photos of the part.
- The part can be designed anywhere in the world where the designing skill available.
- Since there is no need for special skills for production, a 3D printing manufacture close to the plant can supply the product reducing time and logistics cost significantly.
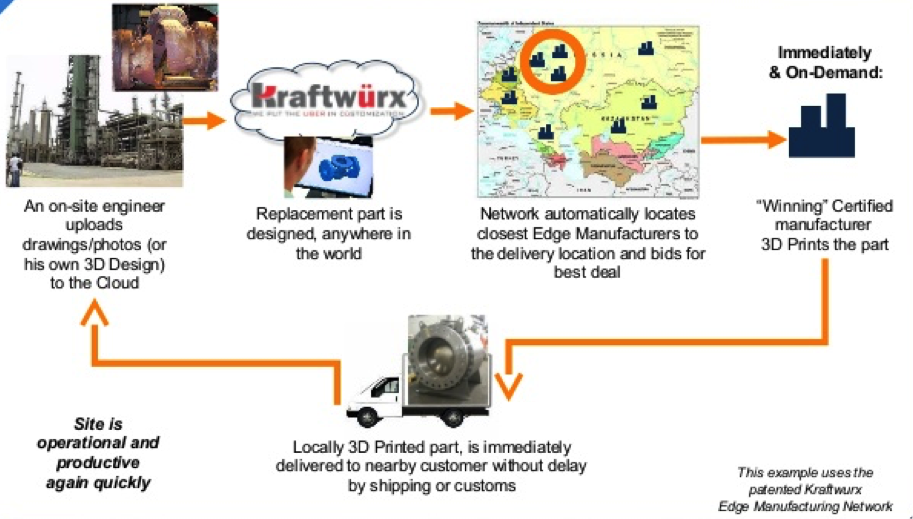
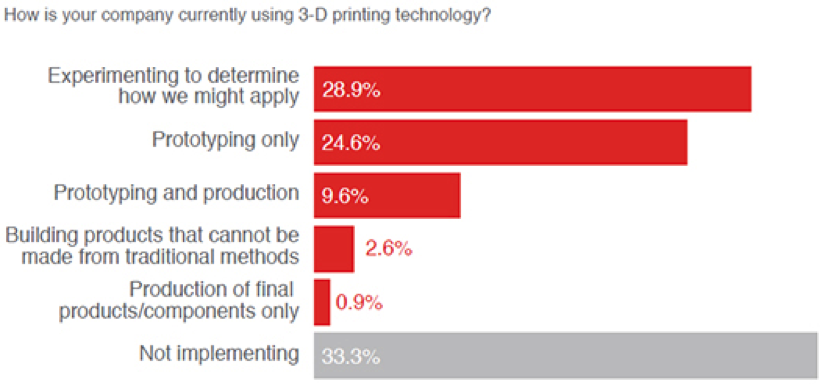