SHARE
Discover the Future of Industrial Automation in Internal Logistics
Increase Productivity when Packing Tubes: The Challenge
In March last year, ennomotive launched a challenge to help a company specialized in the manufacturing of steel tubes increase its productivity through industrial automation. The manufacturing process of steel tubes required too many workers because, at the end of the manufacturing line, tubes accumulate and intertwine with each other before they are taken to the storage location where they had to be manually packed and strapped. The goal of this challenge was to reduce the labor cost in this process by automating the packing process. Ideally, the workers would only feed the installation and pick up the completed packages. For 6 weeks, 47 engineers from 25 countries accepted the challenge and submitted different solutions. After a thorough evaluation, the company picked the solution that best met the evaluation criteria and awarded the winner, the team formed by Eduardo Puente and Alejandro Amo, from Spain. We have contacted Eduardo Puente to learn about his experience and the future of industrial automation. Here you can read the full interview.Eduardo Puente, an industrial automation expert from Spain
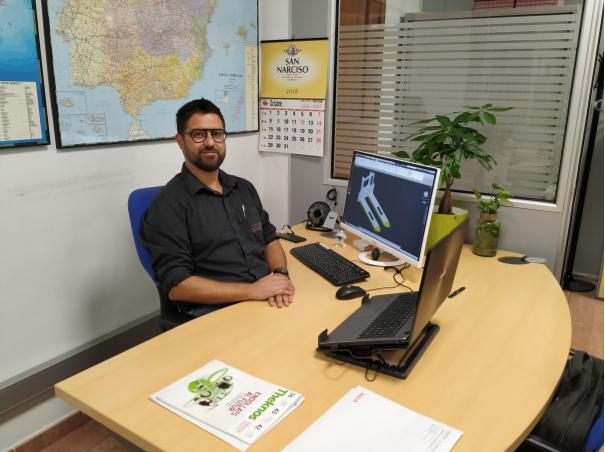
Can you introduce yourself briefly?
My name is Eduardo Puente and I live in Barcelona. I graduated from the Autonomous University of Barcelona (UAB) as an Electrical Engineer, I did a postgraduate programme on Electric Vehicles and other propulsion systems by the Technical University of Catalonia (UPC) and a master on industrial management and organization at the UAB. Ever since I was a child, I have been passionate about my toys' electronic mechanisms and circuits. I remember that, whenever I got one, I used to disassemble it to figure out how it worked. I have 20 years of experience in the industrial sector, more specifically in the metal field.What is your professional background?
When I was 18 years old I started working on Celsa Group as a production worker and, as I saw the years pass by without really growing within the company, I studied an advanced course on automatic control and regulation systems. Once I finished it, I got promoted and I was offered to work on the electrical maintenance unit, which I accepted gladly. At the same time, I continued studying engineering while working shifts, those were some rough years. However, I still remember the immense satisfaction I felt when I graduated, it felt like I could everything I wanted. A few years later, thanks to Enrique Montalbo (my former boss), I got promoted to the company's expeditions department, where I managed the transportations in Spain, Portugal, Balearic Islands, Ireland... Working in that department, I realised that I had learned everything very quickly and there were no challenges for me there, I got bored with the monotony and so I decided to study a postgraduate course on electrical vehicles and other propulsion systems but I did not grow in the company with this curricular complement so I kept studying. This time I started an official master on industrial management and organization. I wanted to thank Elena Gutiérrez (another former boss of mine), who was the person who allowed me this evolution, both professional and personal, within Celsa Group. At some point, I saw that I could not grow any more in that company and so I decided to work for a self-driving car manufacturing company, where I started as a project manager and then evolved to production director. I was in charge of procurement, production, and expeditions until I was offered to lead a new project in a dealer company of a big brand specialized in internal logistics. After putting some thought into it, I accepted and I now lead the Logistic Solutions department of this company, where we offered automated solutions for all kinds of companies, warehouses, production, etc.What projects have been truly important for your career?
The biggest project I participated in was some high capacity trains or trailers that have the ability to switch axis automatically. They are bidirectional, even if the axes are not aligned, and have a capacity for 3.1 Tn. They are independent elements and interchangeable and can be inter-chained to create a convoy of a maximum of 3 wagons (9.3 Tn). With this project, our client multiplied by 2.5 its internal transportation capacity for the leader coffee plant in Europe and second best in the world. This has been the most rewarding project I have done from scratch. The satisfaction comes when you pay them a visit and see the loaded train circulating around the production plant.What groundbreaking advances have been made in industrial automation in the past few years?
In my opinion, it is clear that times are changing and we must move towards a partial automation, in case there is no automation at all. The internal logistics processes of factories add less and less value to the product and, as I always say, if something does not add, it takes away. The interior automated transportation is creating a major change in the companies, no doubt, but the hardest part is always to convince people. How do you tell people that have always pulled a pallet truck that, from now on, that pallet truck is going to transport pallets by itself? That mindset is very difficult to change. Apart from that, new equipment models are emerging, for example, personal ones that reduce the effort at work. I am talking about articulated exoskeletons that are going to be seen everywhere in the coming years, I am sure. Thanks to them, leaves due to injuries will be reduced, which contributes to an increase in productivity too.Is it difficult to innovate in this sector? Why?
It is difficult, especially because every company needs a custom-made project, every company has its particularities and needs. For instance, in a minimally sophisticated system, the information must flow from the client to the automated part and the other way around. In this sense, we usually find that every company has its own IT system to control its processes, which forces us to custom-make them. Another problem when it comes to innovation is the cost. Prices are now very high because the process is crafted by many experts. There is no standard process, so far, which makes it mandatory for a group of people to work on these projects in order to succeed.Which do you think will be the most immediate advances in this sector?
From my point of view, M2M systems are going to experience a tremendous progress everywhere. For example, the trash cans in big cities will inform about their capacity to change the pickup route and thus optimize fuel and minimize pollution. When it comes to traffic, I always think about the empty streets at night and the timed traffic lights that make cars stop even though there is nobody to cross the street. This creates more pollution because stopping and starting up a car again is an unnecessary waste of energy. I don't know, I think somebody should look into these issues that are so easy to solve and have a great impact in a big city like mine, Barcelona. On the other hand, as I mentioned in a previous question, I believe articulated exoskeletons will become huge for HR optimization in companies with a lot of workers. Lastly, I think automatic systems both in logistics and other fields will become part of our environment. My experience in companies is that these systems rarely falter, halt...Share your thoughts with us and explore what else ennomotive has to offer you.