SHARE
Underground Navigation and Mapping on Autonomous Robots
The scientific community has developed a wide variety of new applications in robotics. Most developed robots have been designed to operate in the ground, the sky or the sea, but one field is close to forgotten: the underground. Let's take a look at one amazing autonomous robot with underground navigation, localization and mapping.
BADGER: Underground autonomous robot
We mentioned in a previous post the BADGER (roBot for Autonomous unDerGround trenchless opERations, mapping and navigation), a project launched by the Universidad Carlos III de Madrid in association with other research groups whose goal is to design and develop the BADGER autonomous underground robotic system that can drill, maneuver, localize, map and navigate underground. It will be equipped with tools for constructing horizontal and vertical networks of stable bores and pipelines. The project is still ongoing and it has a promising future.This new system will use innovative techniques of location, mapping and navigation, as well as a wide variety of sensors and a Ground Penetrating Radar that will allow it to adapt to different terrains, which will facilitate the analysis of the different scenarios and the decision-making process during operations.
Underground navigation, localization and mapping.
The robotic concept comprises two main physical subsystems. The first is the underground robot that autonomously tunnels, navigates and executes tasks in beneath the ground. The second is the control console located on the surface, operated by a human. The control console will communicate with the underground robot either through umbilical (wired) connection or wirelessly using repeaters installed along the tunnel. The first subsystem is composed by a drilling head which will be modular allowing replacement depending on the application and the type of the soil, a propulsion mechanism that is equipped with clamping mechanisms and generates peristaltic crawling motion among the modules resulting in a net forwards (or backwards) displacement of the robot center of mass (CM), a steering mechanism, a transportation of cuttings mechanism that will move the cuttings pushed back by the bore-head to the surface by means of a pump, 3D printer that will print a tunnel wall support with additive material and an on-board Ground Penetrating Radar (GPR) to act as active exteroceptive sensor and sense the surrounding environment. All physical components of this subsystem will be integrated into a flexible, modular, multi-segment robot design that can articulate its segments during the drilling process to fit the curved bore. The second subsystem will be composed by a control station that will host the central computer that runs the supervision, planning and monitoring software and a surface radar that will facilitate the initial subsurface mapping process, either in an automatic way or manually. Apart from the potential applications of this robot, BADGER is also looking for an ecofriendly impact in the society. It will enable the transformation of the modern cities, for example, with the construction of new wiring installation and pipelines without the execution of ditches or diversions of traffic avoiding the resulting noise pollution or the pollution associated with the excavation.
As you can see, there are plenty of new applications that are still to be discovered. You can start by joining this community and finding a solution for one of the engineering challenges.
Join our engineering community here
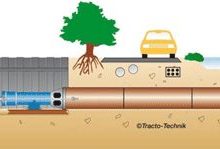
We mentioned in a previous post the BADGER (roBot for Autonomous unDerGround trenchless opERations, mapping and navigation), a project launched by the Universidad Carlos III de Madrid in association with other research groups whose goal is to design and develop the BADGER autonomous underground robotic system that can drill, maneuver, localize, map and navigate underground. It will be equipped with tools for constructing horizontal and vertical networks of stable bores and pipelines. The project is still ongoing and it has a promising future.This new system will use innovative techniques of location, mapping and navigation, as well as a wide variety of sensors and a Ground Penetrating Radar that will allow it to adapt to different terrains, which will facilitate the analysis of the different scenarios and the decision-making process during operations.
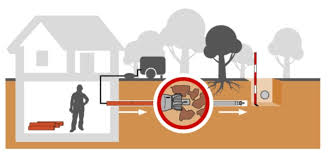
The robotic concept comprises two main physical subsystems. The first is the underground robot that autonomously tunnels, navigates and executes tasks in beneath the ground. The second is the control console located on the surface, operated by a human. The control console will communicate with the underground robot either through umbilical (wired) connection or wirelessly using repeaters installed along the tunnel. The first subsystem is composed by a drilling head which will be modular allowing replacement depending on the application and the type of the soil, a propulsion mechanism that is equipped with clamping mechanisms and generates peristaltic crawling motion among the modules resulting in a net forwards (or backwards) displacement of the robot center of mass (CM), a steering mechanism, a transportation of cuttings mechanism that will move the cuttings pushed back by the bore-head to the surface by means of a pump, 3D printer that will print a tunnel wall support with additive material and an on-board Ground Penetrating Radar (GPR) to act as active exteroceptive sensor and sense the surrounding environment. All physical components of this subsystem will be integrated into a flexible, modular, multi-segment robot design that can articulate its segments during the drilling process to fit the curved bore. The second subsystem will be composed by a control station that will host the central computer that runs the supervision, planning and monitoring software and a surface radar that will facilitate the initial subsurface mapping process, either in an automatic way or manually. Apart from the potential applications of this robot, BADGER is also looking for an ecofriendly impact in the society. It will enable the transformation of the modern cities, for example, with the construction of new wiring installation and pipelines without the execution of ditches or diversions of traffic avoiding the resulting noise pollution or the pollution associated with the excavation.
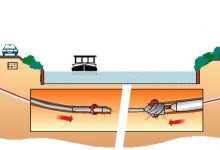