SHARE
Meet the winner Maksym Gaievskyi: "Working Remotely is not a Problem"
One of the winners of the Heavy Lifting Automation Challenge, Maksym Gaievskyi, answered the questions of our interview and told us how he solved the challenge working with a team of engineers, how he felt working on a challenge from the other side of the world, and many more!
Maksym Gaievskyi
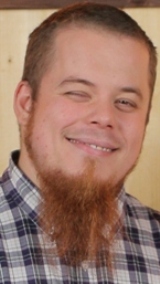
Can you introduce yourself briefly? What is your more relevant working experience?
My name is Maksym Gaievskyi. I live in Dnepropetrovsk, Ukraine. I finished my studies at the National Mining University and I specialize in Mechanical Engineering and Machine Building Technology.
When I was a student (the 2nd course, 19 years old) I began to work at the plant as a student of the operator CNC. The main specializations of the plant are hydraulic equipment and equipment for aviation fuel systems. I understood that it was the best way to get the necessary knowledge and practical skills on how to produce parts, machining, welding, bending, cast molding, etc.
When I was working at the plant, I got skills on how to use different measuring tools, how to design difficult technological equipment for machining, welding, measuring tools and etc. It was the perfect experience because you can work closely with the best engineers and technologists, and I always got full answers to my questions. Of course, working at the plant helped me to study faster because I had already had a more practical experience compared to my classmates. Halfway through my 5th year, I got a proposition to work at the engineering department of that plant. At that moment I realized that it was a great chance to start my career as an engineer.
I can't say I liked it at first because I didn't get PC, but I got 2 very old and experienced mentors. At that moment I didn't understand why I couldn't design without having to learn so many standards. The plant also has a military technical Commission, so all developments, drawings, and finished products have increased control at all stages, which is why I needed to know standards for the designing of difficult equipment, typical technical solutions, norms, and rules. Today I know it was necessary for forming the first skills in a young engineer, plus it has given me discipline and order in the work.
This plant was the starting point for my engineering career. After he had a couple of firms in Lviv and Kiev. Then I was offered a contract in China for a year to design the tow trucks. After China there was a firm in Ukraine, then again a contract in Bulgaria for designing elevators.
At present day I work for the company in Ukraine and have been working as a freelancer for a few years. Thank God, my professional experience, and this metallurgical industry, heavy machinery, lifting mechanisms, hydraulic units, furniture production, electrical production, allows me to work in different sectors. Unfortunately, there are engineers able to work quickly in Solidworks, NX or Catia, but with a poor understanding of how to make a product. For this reason, the cost of components is often overpriced, in my opinion.
What challenges have you participated in? How well did you do in them?
My first challenge was Heavy lifting automation system and the second was Measuring tool for railway production. The first challenge was very interesting for me. I started to work on it after reading the answers from the client and I realized that other engineers tried to solve one or two problems that would help solve it only locally. I saw the solution to the client's problems only in an integrated approach, solving every problem.
What kind of challenge do you like most? Why?
I like different kinds of challenges, but I try to choose them depending on what's interesting to me. I like to design non-standard equipment when there is a low budget or, even worse, you have to design the perfect product with no budget. In this case, very interesting solutions can be born.
What is your motivation for participating?
My motivation for participating is my interest and my drive to try something new and gain new skills. When you try to solve a challenge, you have to read a lot of information before you design your idea based on solid knowledge. I think that participating in an engineering challenge is perfect for personal growth and gaining new technical skills. It is not worth it if you only do it for the money, which can be a tool but not the main target.
At the same time, I see that everyone who spends a lot of time working on a challenge wants to have not only personal satisfaction but also a good payment for a job well done. Everyone can decide before starting the participation in the challenge.
Did you have any experience with this kind of challenges? Have you solved a similar challenge in the past?
Yes, I have a lot of experience with lifting systems and mechanization of handle jobs.How did you come up with this solution? What was your inspiration?
My first idea was that I needed to help the workers to stop lifting tubes all day because it is physically challenging. These thoughts didn't allow me to sleep well because I was working at the plant in the workshop, and I know how hard it is sometimes to lift up technological equipment for machining and set up after on CNC. Bearing in mind that it was necessary to solve the issue of simplification or replacement of manual labor by mechanization or automation while maintaining the scope of the established budget for the project, I began to work.
You were a member of the group that delivered the solution. What are the benefits of participating as a group?
Yes, I was a member of the group but not at first, it was an interesting situation. I received the e-mail that said that I moved on to Round 2, and I only had a month for the design. I was very busy with my job in Bulgaria and I needed to submit a detailed design for the challenge. The situation was critical, I really didn't have time.
I started calling my colleagues with whom I had worked before and offered cooperation. By the way, as it turned out, the habit to observe the colleagues and the way they solve work tasks proved to be very useful in this case because it helped to remember the most talented and capable engineers with whom I have a connection to this day. I called one of my friends, who happened to be very busy, but he offered to tell his father, also a very talented designer, who became interested, and we started working as a team. We revamped the original concept, and further simplified and significantly reduced the cost, but at the same time remaining true to the original idea.
What are the benefits of participating as a group? There is an old saying - one head is good, but two is better. My colleague, based on his own experience, offered some good comments on the original concept, and I was able to review and finish the gripping mechanism, which was my friend's idea initially.
How was working remotely for a foreign company? Would you do it again?
Working remotely is not a problem, it does not matter from which country the client comes from. To me, there are 3 important aspects in this case: obtaining correct and clear technical requirements, the decency of the client, and the speed of receiving answers from the client to the necessary questions.
Although we must admit that, sometimes, the language of communication plays an important role with customers. For example, there were cases when the client didn't speak English and, for this reason, there were difficulties in understanding each other.
Regarding the issue of continuing cooperation. Why not? I am sure that this company has a number of issues and bottlenecks in the production and our experience could be useful to them. I am always open to honest and mutually beneficial cooperation.
How is the manufacturing industry in Ukraine? What is the degree of automation there? Where do you see the industry heading towards in the future?
Ukraine's manufacturing industry is not developing as quickly as we would like, but there are certain movements. There are two main factors that slow down the manufacturing industry's growth, the conflict in the East of the country and the prices of raw materials and energy resources in the world market. All this affects the national economy, and therefore the country's industry. Many may think that everything is bad there, but it is not as it seems initially. Over the past few years, the country has had very interesting start-up companies. Of course, these are not huge factories, but there is some development.
I have a very specific attitude towards automation. I am a supporter of automation because, after all, the most important thing is the final cost for the ordinary buyer and quality. I understand that now it is the time when people are chasing a big profit, equipped with robots and manipulators, hoping to show how innovative they are, how good their products are, even when the price is too high.
I see an increase in automation but, unfortunately, the quality of the products is getting worse every year. The question is: why is this happening? At its core, automation should accelerate production and make the worker's job easier while increasing the quality of the products. Of course, this statement does not apply to all companies, but my experience showed me that now, the number of released products is more important than quality.
With confidence, I can say one thing: the future is not for automation, but for qualified engineers, the deficit of which is now observed in almost any country. As the Biblical wisdom says: "whoever prepares in advance is wise."
Thank you for the interview and your time. It was nice meeting you and I hope that in the future we will cooperate.